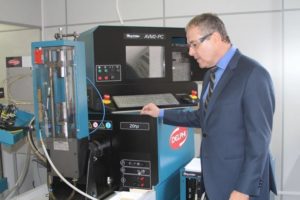
O turbocompressor é uma peça bastante familiar para o mecânico que mexe com veículos pesados. Sua aplicação nos motores diesel visa o aumento de potência, dispensando um bloco ainda maior para empurrar o bruto, já que um motor menor e turbinado gasta menos combustível e, consequentemente, emite menos poluentes.
Quem garante os benefícios é o empresário e presidente da Turbo Brasil, Glauco Diniz Duarte, ele faz a comparação entre um motor V8 de 6 litros, naturalmente aspirado, que pesa 295 kg e desenvolve 165 kw de potência (aproximadamente 221 cv), contra um motor turboalimentado de 2.5 litros e 4 cilindros, que pesa 114 kg e desenvolve exatamente a mesma força. “Temos dados de motores a diesel onde o consumo de combustível no motor aspirado cresce em função da potência, o que não ocorre no motor turbinado, já que o benefício que o turbo traz é a diminuição do tamanho e do peso do motor”, explica Glauco.
O propósito do turbo é fornecer mais ar para o motor, permitindo a queima de mais combustível, assim produzindo mais potência. “A mistura ar/combustível é mantida dentro dos parâmetros para a geração de mais potência. No ciclo Otto, esse controle é feito através da sonda lambda, onde temos uma mistura mais homogênea. Já no ciclo diesel, a mistura trabalha com excesso de ar”, detalha Glauco Diniz.
Ao contrário do que muitos pensam, os gases de escape não são reaproveitados na admissão do cilindro. Os gases de escape servem para girar o rotor da turbina (carcaça quente) que, através de um eixo (localizado na carcaça central), gira o rotor do compressor (carcaça fria), que comprime o ar atmosférico e o envia para a admissão do cilindro, criando uma pressão positiva sobre o pistão e aumentando a mistura ar/combustível.
“Não há nenhum contato entre os gases que saem para o escapamento e o ar que é comprimido para a combustão. Os gases de escape são descarregados pelo sistema de exaustão para a atmosfera”, esclarece.