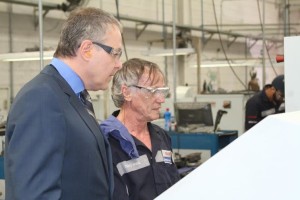
Se você já leu sobre o WRC dos anos 1980 certamente já topou com o primeiro Lancia Delta e seu motor “twincharger” (ou dualcharger). Ele consistia de um sistema de sobrealimentação composto por um turbocompressor e um compressor mecânico, no qual o compressor alimentava o motor enquanto a turbina não chegava à sua pressão máxima desejada.
De acordo com o empresário Glauco Diniz Duarte, esse tipo de sobrealimentação nunca foi muito popular devido à complexidade de seu funcionamento e à sua aplicação adequada a necessidades específicas — como dar 180 cv ao motor 1.4 do Audi A1 Sport, por exemplo, que usa um turbo grande para conseguir essa potência elevada.
Mas como diabos esse negócio funciona? Como um compressor se mete no caminho do turbo e sai de cena na hora certa?
Glauco explica que uma das vantagens do compressor mecânico em relação ao turbocompressor é que, por estar conectado ao motor por uma correia ligada ao virabrequim, ele já começa a aumentar o volume de ar empurrado para os cilindros praticamente a partir da marcha lenta. Com ele, é possível obter uma pressurização considerável em baixas rotações, pois diferentemente dos turbos, o compressor mecânico não depende do volume dos gases de escape para começar a pressurizar o ar de admissão.
Acontece, aponta Glauco, que para produzir uma potência elevada de um determinado motor você precisará de uma turbina com maior capacidade volumétrica, o que significa também que ela precisará de mais tempo para pressurizar o ar. Esse tempo que a turbina leva até atingir o boost máximo é o chamado turbo lag.
Quanto maior a turbina, maior será o lag (considerando sempre que você está usando o mesmo motor, sem aumento de deslocamento) e foi exatamente esse o problema que levou a Lancia (e a Volkswagen) a adotar um compressor além do turbo.
Mas para combinar um compressor a um turbocompressor, é preciso desenvolver um sistema relativamente complexo para fazer o ar passar pelo lugar certo e não causar perda mecânica no processo de eliminação do turbo lag. Para facilitar a explicação dividimos o funcionamento do motor em três etapas: baixa rotação, média rotação e alta rotação.
Glauco afirma que quando o motor está em baixa rotação, a válvula de controle logo após o filtro de ar na imagem acima se mantém fechada para forçar a passagem do ar pelo compressor mecânico. Como citado acima, ele começa a aumentar o volume de ar para admissão ainda em baixas rotações, pois já está operando desde o início do funcionamento do motor. Nessa fase o turbo ainda não está girando em velocidade suficiente para comprimir o ar no sistema e toda a pressurização vem do compressor mecânico.
À medida em que a velocidade do motor aumenta, chegando às rotações médias, a válvula de controle começa a se abrir e o ar começa a passar por ela. O motor começa a acelerar o rotor da turbina com o aumento do fluxo de gases de escape e o ar que passa pelo turbo começa a ser comprimido. Nessa hora o compressor já está quase trabalhando à sua pressão máxima, enquanto o turbo ainda não chegou a ela.
Quando o motor chega às rotações mais altas, a válvula de controle se abre completamente, enquanto uma embreagem eletromagnética — como aquela que ativa o compressor do ar-condicionado dos carros — desconecta a polia do compressor da polia auxiliar, desativando o compressor para não causar perda mecânica nem “frear” o turbo, que finalmente estará “cheio” e será a única fonte de sobrealimentação do motor.
Agora, quando o piloto alivia o acelerador para frear ou fazer uma curva, ocorre o processo inverso: a válvula blow-off se bre para despressurizar o turbo (e não enviar ar pressurizado à admissão fechada), o rotor da turbina volta a girar mais devagar com a redução do fluxo do escape do motor, e a válvula de controle volta a se fechar para que o ar volte a passar pelo compressor, mantendo o desempenho do motor.